Habermann Aurum Pumps GmbH has successfully carried out a customized adaptation of the pumps and the installation of the vertical pumps NPK 250/630 V2 with a shaft length of 4,100 mm in the thermal power plant. The pumps previously used by the customer in the facility required annual maintenance, including the complete replacement of hydraulic components and the sealing unit. Additionally, the complex and time-consuming process of aligning the shaft resulted in high time and cost expenses. The costly downtime of the facility was a crucial factor for the customer to consider optimization possibilities.
By using the vertical Habermann Aurum pump with a solid shaft and the proven HGD mechanical seal, the maintenance effort and downtime due to failures were minimized. Since its initial deployment in December 2021, the NPK 250/630 has been operating with utmost reliability. It operates 24/7 without any interruptions. This is yet another example of effective and reliable technology from Habermann, even when dealing with highly abrasive and corrosive media, such as ash-laden suspensions.
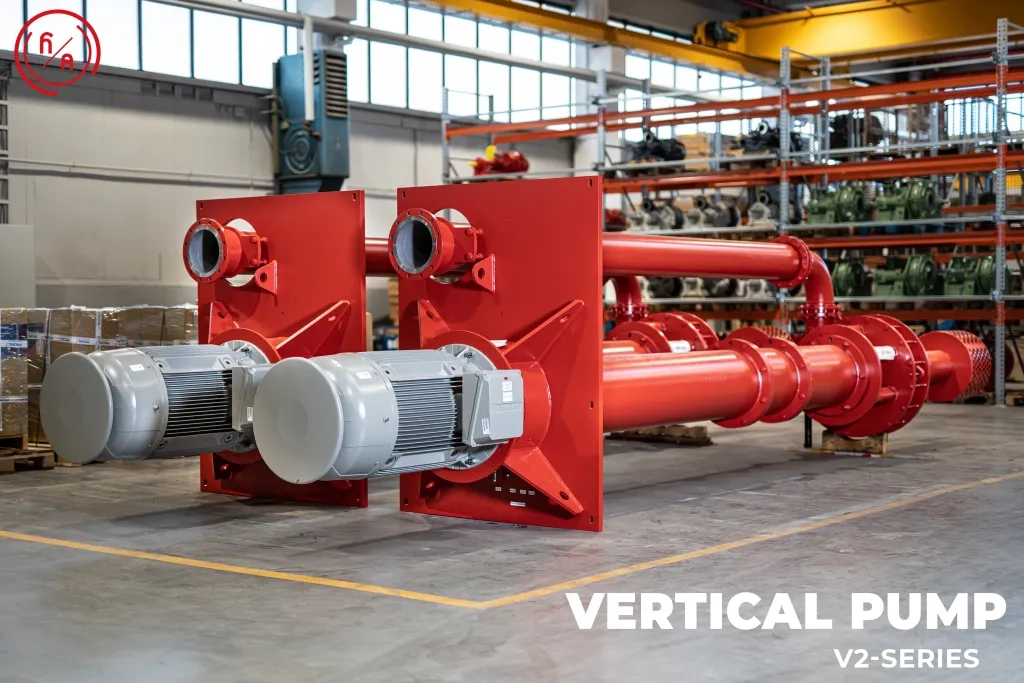
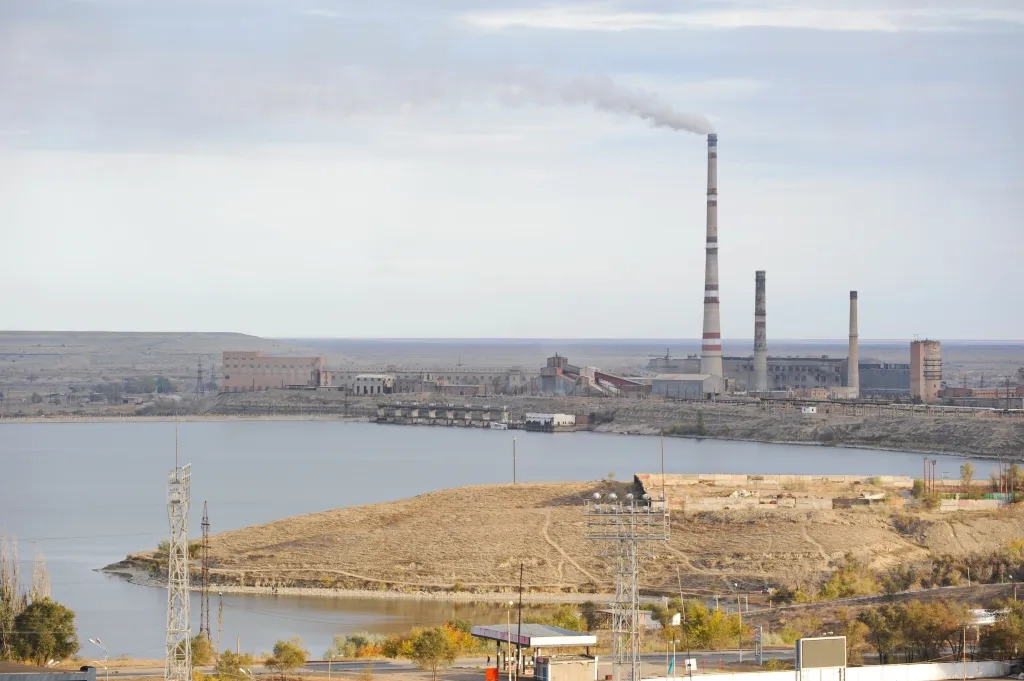
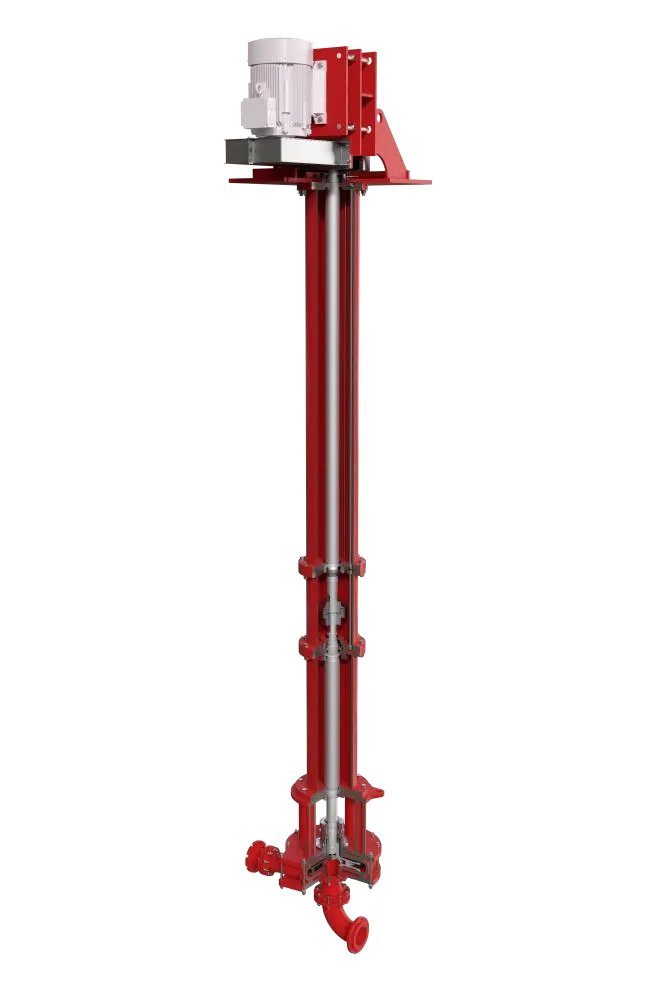
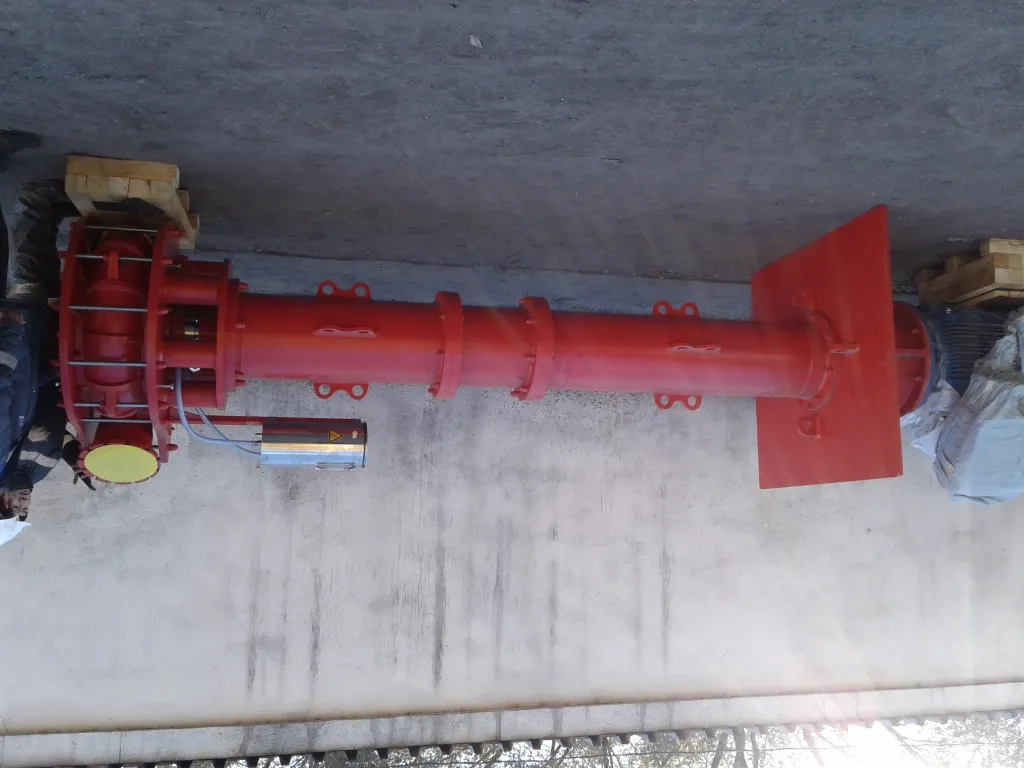
Working for Habermann Aurum Group
Our company speaks to serve all continents
Average lifetime of Habermann slurry pumps
is the oldest running pump in the factory
Where our pumps are in daily use
We are one of Germany's leading manufacturers of centrifugal pumps
Why Habermann Aurum Pumpen?
Habermann Aurum Pumpen is one of the leading manufacturers of centrifugal pumps for handling solids-laden liquids. With almost 100 years of experience and an expertise of over 30,000 pumps in use worldwide in a wide range of industrial sectors, we have become part of the global economic system. Our product portfolio includes pumps and valves. Thanks to our in-house engineering, we are also able to solve technically demanding and complex tasks. Our fundamental goal is to develop the most durable and sustainable industrial pumps by combining decades of experience with the latest technology. Our pumps are used in mining and the mineral industry, raw material extraction and the energy industry, the steel industry, chemicals, pigment industry, tunnelling and special civil engineering.