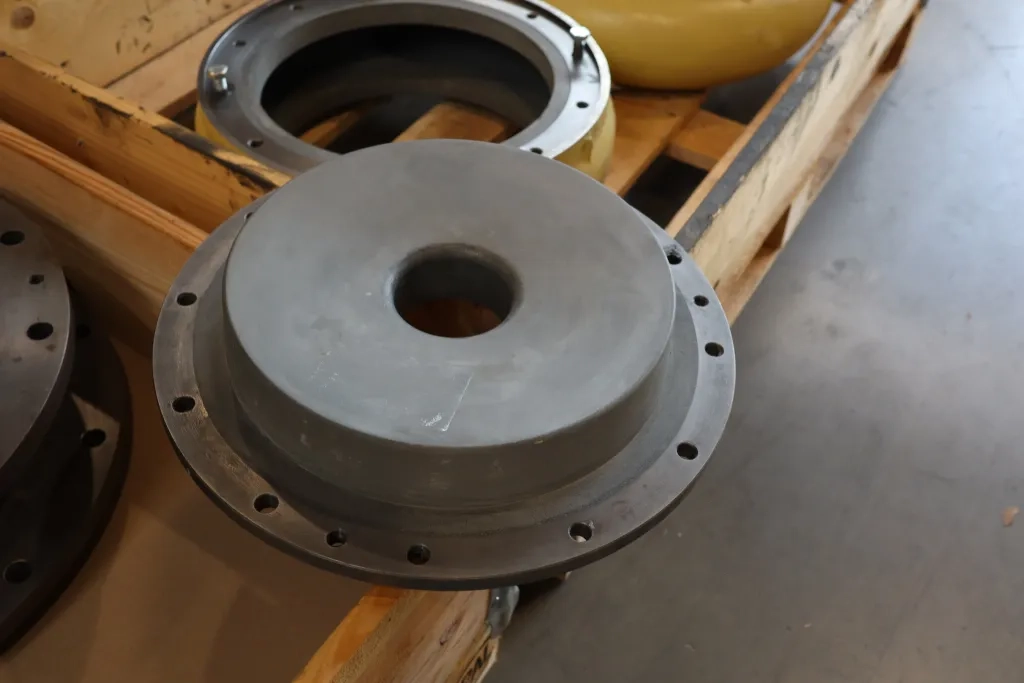
We have been building pumps for almost 100 years, and since that time we have been committed to combining experience, expertise and innovation. Time and again, we have been able to introduce world firsts to the market. And the fact that we are still living up to this claim today is shown by the continuously increasing worldwide demand for our products. We are proud to report that our pumps are valued for their robustness and durability, among other things. But what is the reason for this? What are the secrets of Habermann Aurum pumps? There is one we want to reveal today. And that is the following: In the case of our HPK solids handling pumps, it's because of a special material and its use: ceram carbide.
What is Ceram Carbide?
Ceram Carbide is the cast polymer lining of these slurry pumps. It is a non-metallic composite material consisting of more than 80% silicone carbide and the remaining nearly 20% venil ester resin binder. Why we choose this combination? Quite simply, silicon carbide is a non-oxide ceramic. It is the lightest, but at the same time the hardest ceramic material. By comparison, its hardness is almost as hard as that of a pure diamond. As a result, silicon carbide has very good resistance to acids and alkalis and is resistant to wear and corrosion even at high temperatures of up to 200 degrees Celsius. Vinyl ester resins, on the other hand, are synthetic resins that form thermosetting plastics of high strength and chemical resistance when cured. They are therefore frequently used in the manufacture of glass fiber reinforced plastics, i.e. in chemical apparatus engineering, process engineering, highly chemical and thermally stressed equipment, among others.
What makes Ceram Carbide so robust?
We developed this unique composition of Ceram Carbide polymer castings together with our partners. It ensures that our Ceram Carbide-lined slurry pumps can be used in particular in the chemical industry, for example in the desulfurization of analogs and in mineral processing plants. However, the outstanding robustness of Ceram Carbide compared to other polymer castings means that fine-grained solids can also be pumped. And: Ceram Carbide is resistant to materials at temperatures of up to 200 degrees Celsius - no other polymer casting can withstand comparable temperatures.
How do we use Ceram Carbide?
Unlike our competitors, we do not use polymer casting as a monoblock. This is because in order to then connect the corresponding pump housing to it, sealing points would have to be drilled into the block, which would make it easily brittle and could tear, so that operational safety would no longer be guaranteed under any circumstances, especially when working with hazardous chemical substances. For this reason, its use would also be limited to only particularly fine-grained solids. Also, the pumps connected to the monoblock could not be repaired afterwards - on the contrary, the entire plant would have to be replaced. This is neither sustainable nor efficient.
Why are pumps equipped with Ceram Carbide particularly durable?
That's why we cast the Ceram Carbide into the one-piece metallic outer casing. We use vacuum casting, which means that there are no oxygen deposits and the casting is free of spores. This alone allows us to significantly increase the resistance of the finished pump. At the same time, the HPK series of slurry pumps equipped with Ceram Carbide are still very compact and are produced as double-casing pumps in composite design. In other words, they consist of a one-piece outer casing completely cast in metal and with the firmly cast inner casing groove described above, wear covers that can be replaced separately on the suction and drive sides, an open, three-bladed impeller in an inclined design, and Aurum Habermann's proven shaft seal. The resulting compatibility with all slurry pumps of the series thus also enables all necessary repair and replacement work to be carried out if required, resulting in the unique longevity of our pumps, which is appreciated worldwide.
Further advantages of our pumps
However, in addition to the resulting pumping strength and sustainability, the robustness and durability have even further positive consequences for our customers. This is because they enable us to guarantee a high level of operational and occupational safety even in chemically demanding processes. And, as already mentioned, it also prevents the cracking familiar from monoblocks. For customers in the chemical industry, this is a unique offer. After all, we are convinced that no other pump can handle fine-grained solids and minerals to be processed so well, and, if necessary, desulfurize them so reliably and safely.
We remain true to our line
The development of this most efficient use of Ceram Carbide makes us proud. And we know that, as mentioned at the beginning, we owe it to the experience and expertise of our employees and the resulting innovative strength. This is also the basis for another key aspect of our HPK series offering: our sales and service experts, who are active around the globe, immediately understand which pump in the series can be used in the best possible way by our customers, how their system can be optimized if necessary, and how repairs can be carried out quickly and cost-effectively if necessary. Their service performance is unique. For example, our employees speak ten languages as their mother tongue, ensuring the greatest possible understanding and smooth communication in consultation from the initial contact and throughout the entire service life of the system. And even for plants from sectors other than the chemical industry, they can find tailor-made and state-of-the-art solutions.
Always at the cutting edge - as has been the hallmark of Habermann Aurum Pumpen for almost 100 years and will continue to be so in the future.